The Role of Auto Molds in Modern Metal Fabrication
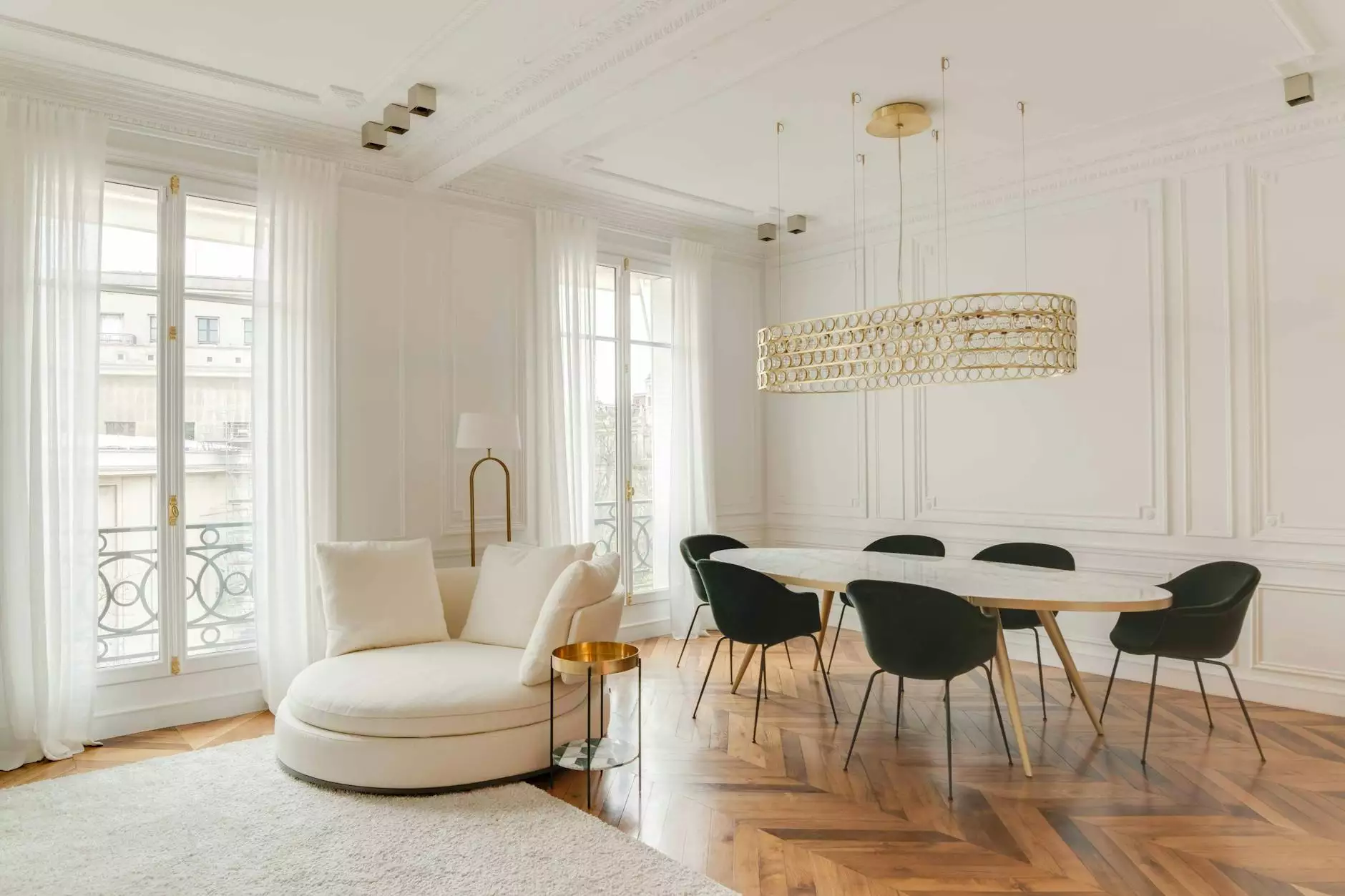
Auto molds play an indispensable role in the automotive manufacturing process, acting as the backbone for a wide array of components that make up modern vehicles. From the intricate details of a car door to the robust framework of the chassis, the design and precision of auto molds determine the quality, efficiency, and affordability of automotive production. This article aims to provide an exhaustive overview of auto molds, particularly their applications in metal fabrication.
What Are Auto Molds?
In the automotive industry, the term "auto molds" refers to specialized molds used in the production of parts and components for vehicles. These molds are typically crafted from high-grade materials that can withstand extreme conditions, making them suitable for a variety of manufacturing processes.
Types of Auto Molds
Auto molds can be categorized based on their manufacturing techniques and materials used:
- Injection Molds: Most common in the automotive industry, these are used for creating plastic components. They're essential for producing parts like dashboard panels and light fixtures.
- Compression Molds: Often used for rubber components, compression molds are ideal for producing parts like gaskets and seals that require compressive strength.
- Blow Molds: Specifically designed for hollow parts, these molds are used to manufacture items such as fuel tanks and other storage solutions.
- Die Casting Molds: Used for metals, die casting molds are crucial for creating components such as engine blocks and transmission housings.
The Importance of Precision in Auto Molds
Precision is paramount in the production of auto molds. Any deviation in dimensions can lead to significant issues in the final product, including:
- Increased production costs due to remanufacturing.
- Potential safety hazards for vehicle operators.
- Decreased consumer satisfaction due to product failures.
Advanced Technologies in Auto Mold Production
With technological advancements, the production of auto molds has evolved dramatically. Technologies such as Computer Numerical Control (CNC) machining and 3D printing are revolutionizing how molds are designed and manufactured.
Computer Numerical Control (CNC) Machining
CNC machining allows for remarkably precise cuts and shapes, facilitating the creation of complex mold designs. This technology enhances repeatability and reduces the risk of human error during the manufacturing process.
3D Printing in Auto Molds
3D printing is emerging as a game-changer in the industry. It enables rapid prototyping of mold designs, allowing manufacturers to create and test molds much faster. This not only speeds up the production process but also allows for more innovative designs without the high costs associated with traditional manufacturing methods.
Materials Used in Auto Molds
Choosing the right material for auto molds is critical. The selection can affect not just the performance of the mold, but also the end product’s durability and functionality. Common materials include:
- Steel: Known for its strength and durability, steel is preferred for high-volume production where longevity and precision are a must.
- Aluminum: Lightweight and cost-effective, aluminum molds are ideal for lower production runs and complex designs.
- Composites: Used in specialized applications, composite materials are often utilized for parts requiring a low weight to strength ratio.
The Process of Creating Auto Molds
The creation of auto molds involves several key steps:
1. Design
It all starts with a detailed design. Engineers and designers collaborate to create 3D models that outline every aspect of the desired mold.
2. Prototyping
Using technologies like 3D printing, manufacturers can create prototypes to ensure the design meets all specifications and requirements.
3. Production
Once the prototype is approved, the production phase begins. This often involves CNC machining or traditional machining methods to produce the final mold.
4. Testing
Before full-scale production, molds undergo rigorous testing to ensure they can withstand operational stresses.
5. Continuous Improvement
Following production, manufacturers often collect data and feedback to refine mold designs and production processes continuously.
Challenges in Auto Mold Production
The production of auto molds is not without its challenges. Industry players must navigate various issues, including:
- Cost Management: Balancing quality and affordability is essential, especially in a competitive market.
- Technological Adaptation: Keeping up with rapidly changing technologies and methodologies can be overwhelming for some manufacturers.
- Supply Chain Disruptions: Global events can impact the availability of raw materials and components necessary for mold production.
Future Trends in Auto Molds and Metal Fabrication
As the automotive industry continues to evolve, the future of auto molds looks bright. Trends such as:
- Electric and Autonomous Vehicles: The rise of electric vehicles (EVs) and autonomous driving technology is creating new demands for innovative mold designs.
- Eco-friendly Materials: Manufacturers are exploring renewable and recyclable materials to minimize their environmental footprint.
- Smart Manufacturing: The integration of IoT and AI is expected to enhance the efficiency and precision of mold manufacturing processes.
Conclusion
In conclusion, auto molds are a vital element of the metal fabrication sector, influencing every aspect of automotive production. As technology advances and new materials are developed, the capabilities of auto molds are expanding, paving the way for innovation in vehicle design and manufacturing. For companies in the automotive industry, investing in high-quality mold production techniques is not just a strategic advantage but a necessity in a rapidly evolving market.
By embracing the latest technologies, maintaining a focus on precision, and adapting to changing consumer demands, businesses can ensure that they remain at the forefront of the automotive manufacturing landscape. At DeepMould.net, we leverage advanced techniques to deliver superior auto molds that meet the industry's highest standards, ensuring our clients' success in this competitive arena.