Exploring the Benefits of OEM CNC Turn Parts Factory
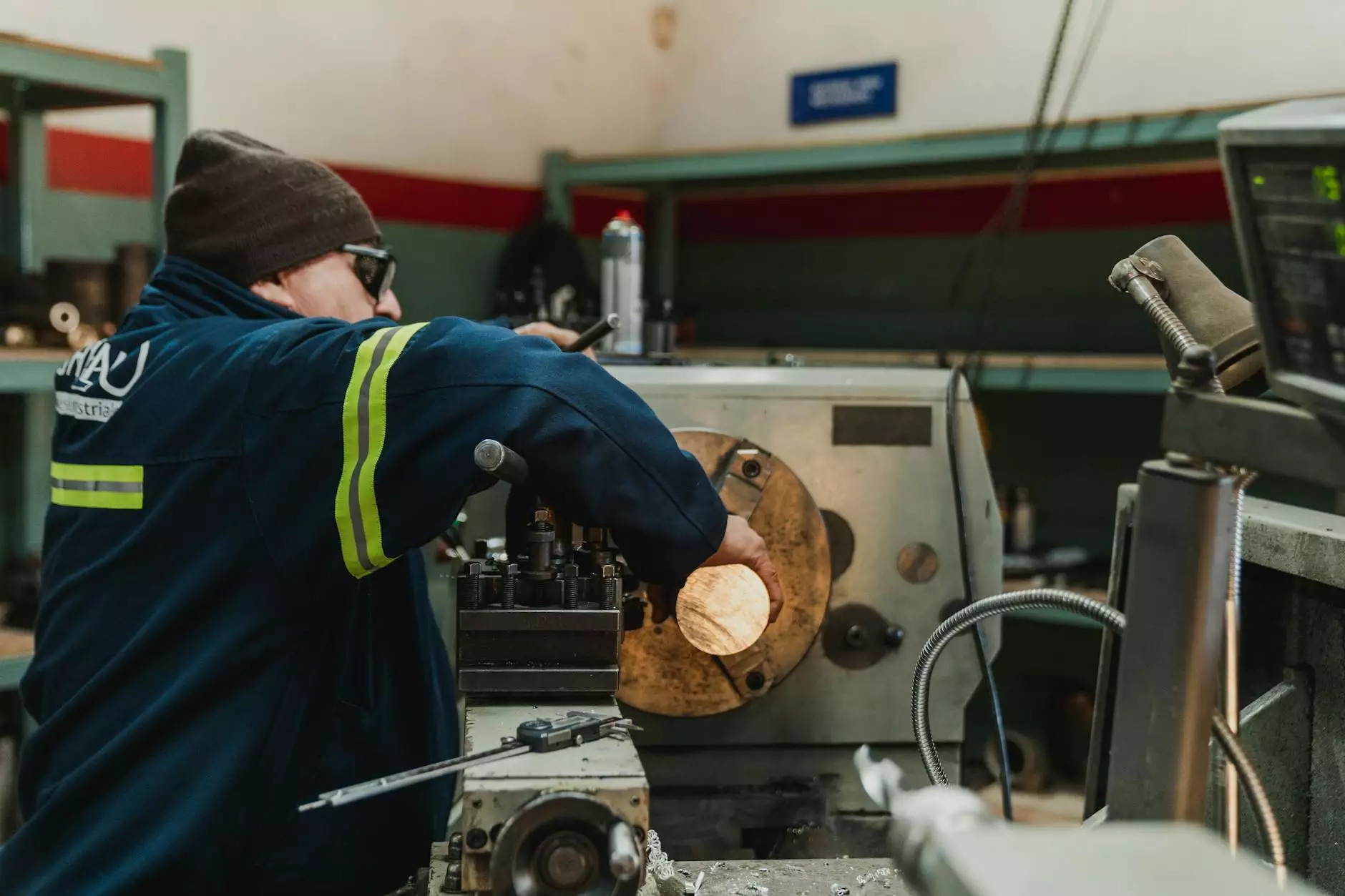
The modern manufacturing landscape is more dynamic than ever, and one key player in this evolution is the OEM CNC turn parts factory. These facilities exemplify the principles of precision engineering and lean manufacturing, helping businesses streamline their processes and enhance product quality. In this article, we'll delve into the myriad advantages of partnering with an OEM CNC turn parts factory, particularly for those in the metal fabrication industry.
What is an OEM CNC Turn Parts Factory?
An OEM CNC turn parts factory specializes in manufacturing components through Computer Numerical Control (CNC) turning processes. This technology allows for the precise machining of parts from various materials, ensuring consistency and high quality across production runs. OEM, or Original Equipment Manufacturer, signifies that these factories produce components that are integral to the product lines of their clients. Such facilities often cater to various industries, including automotive, aerospace, electronics, and more.
Advantages of Utilizing an OEM CNC Turn Parts Factory
1. Precision Engineering
Precision is paramount in manufacturing, especially when it comes to performance-driven sectors. An OEM CNC turn parts factory employs advanced CNC machines capable of achieving tight tolerances that traditional machining methods cannot match. This level of accuracy ensures that every part fits perfectly within assemblies, reducing the risk of malfunction and enhancing overall product reliability.
2. Increased Efficiency and Productivity
With the automation offered by CNC technology, production times are significantly reduced. An OEM CNC turn parts factory can operate multiple machines simultaneously, leading to higher output rates without sacrificing quality. This operational efficiency translates into faster turnaround times for clients, allowing them to meet market demands more effectively.
3. Cost-Effectiveness
While the initial investment in CNC machinery may be substantial, the long-term savings are manifest. Reduced labor costs, minimized waste through precise machining, and shorter production cycles make partnering with an OEM CNC turn parts factory a financially savvy decision for many businesses. Additionally, bulk production capabilities can lead to economies of scale that further drive down costs.
4. Flexibility and Customization
One of the standout features of an OEM CNC turn parts factory is its ability to adapt to custom specifications. Whether it is altering dimensions or machining components from unique materials, these factories provide tailored solutions that meet the specific needs of their clients. This flexibility is invaluable in industries where innovation and customization are crucial to staying competitive.
5. Material Versatility
OEM CNC turn parts factories are adept at working with a wide range of materials, including metals like aluminum, brass, stainless steel, and titanium, as well as various plastics. This versatility allows businesses to select the most appropriate materials for their applications, optimizing performance while ensuring durability. The expertise offered by these factories also extends to understanding the properties of materials, ensuring the best machining practices are employed.
6. Quality Control
Quality assurance is a critical aspect of manufacturing. An OEM CNC turn parts factory typically implements stringent quality control measures throughout the production process. By employing advanced inspection techniques—such as automated optical inspection (AOI) and Coordinate Measuring Machines (CMM)—these facilities ensure that every part produced meets the specified standards. This commitment to quality leads to enhanced customer satisfaction and trust.
How to Choose the Right OEM CNC Turn Parts Factory
With numerous options available in the market, selecting the right OEM CNC turn parts factory is crucial. Here are several factors to consider:
- Certifications: Ensure that the factory holds relevant industry certifications such as ISO 9001, which reflects high standards in manufacturing and quality management.
- Equipment and Technology: Investigate the type of machinery and technology used in the factory to ensure they utilize state-of-the-art CNC equipment.
- Expertise and Experience: Look for facilities with a proven track record in your industry. Experienced manufacturers are often better equipped to handle complex designs and materials.
- Lead Times: Assess the factory's ability to meet your production deadlines. A reliable partner can accommodate urgent requests without compromising quality.
- Communication: Choose a manufacturer that prioritizes clear communication. Transparency in the production process enhances collaboration and leads to better outcomes.
Case Studies: Successful Partnerships with OEM CNC Turn Parts Factories
To illustrate the benefits of working with an OEM CNC turn parts factory, let's explore a few case studies:
Case Study 1: Automotive Component Manufacturer
An automotive parts manufacturer experienced difficulties sourcing precision-engineered components for their new engine model. After partnering with an OEM CNC turn parts factory, they benefitted from:
- Improved Tolerances: The manufacturer achieved a 0.005” tolerance level, significantly better than their previous supplier.
- Faster Lead Times: Production lead times reduced from 8 weeks to just 4 weeks, enabling rapid deployment to market.
- Cost Reductions: Streamlined processes led to a decrease in production costs by 20%.
Case Study 2: Aerospace Industry Enhancement
A leading aerospace company needed lightweight yet durable components for their latest aircraft. By collaborating with an OEM CNC turn parts factory, they achieved:
- Material Innovation: Introduction of advanced aluminum alloys, enhancing the aircraft's fuel efficiency.
- Custom Design Capability: The factory was able to adapt designs quickly based on aerodynamic simulations
- Strict Adherence to Standards: Compliance with aerospace quality standards was maintained, ensuring the safety and reliability of components.
Challenges and Solutions in Working with OEM CNC Turn Parts Factories
While there are numerous benefits to partnering with an OEM CNC turn parts factory, businesses might encounter challenges along the way. Here’s how to address them:
Common Challenges
- Communication Gaps: Misunderstandings can arise if expectations are not clearly communicated. It's essential to engage in regular discussions and updates throughout the production cycle.
- Quality Inconsistency: Not all factories maintain the same standards. Conduct thorough due diligence before selecting a partner and consider site visits for firsthand insights.
- Production Delays: Unforeseen issues can lead to delays. Have contingency plans in place and establish a strong working relationship with your factory to manage expectations.
Conclusion: Elevate Your Manufacturing with OEM CNC Turn Parts Factory
In summary, engaging with an OEM CNC turn parts factory presents significant opportunities for businesses within the metal fabrication sector. From precision engineering and enhanced efficiency to customization and rigorous quality control, the advantages are undeniable. As market demands continue to evolve, these factories empower companies to adapt, innovate, and excel.
For businesses looking to improve their manufacturing processes and product quality, collaborating with a reputable OEM CNC turn parts factory could be the strategic move that catalyzes growth and success in a competitive landscape. Explore your options today and unlock the full potential of your manufacturing capabilities.
Visit DeepMould.net to learn more about how we can assist you with your CNC turning needs.