Transforming Metal Fabrication with Advanced Electric Injection Machines: A Complete Industry Guide
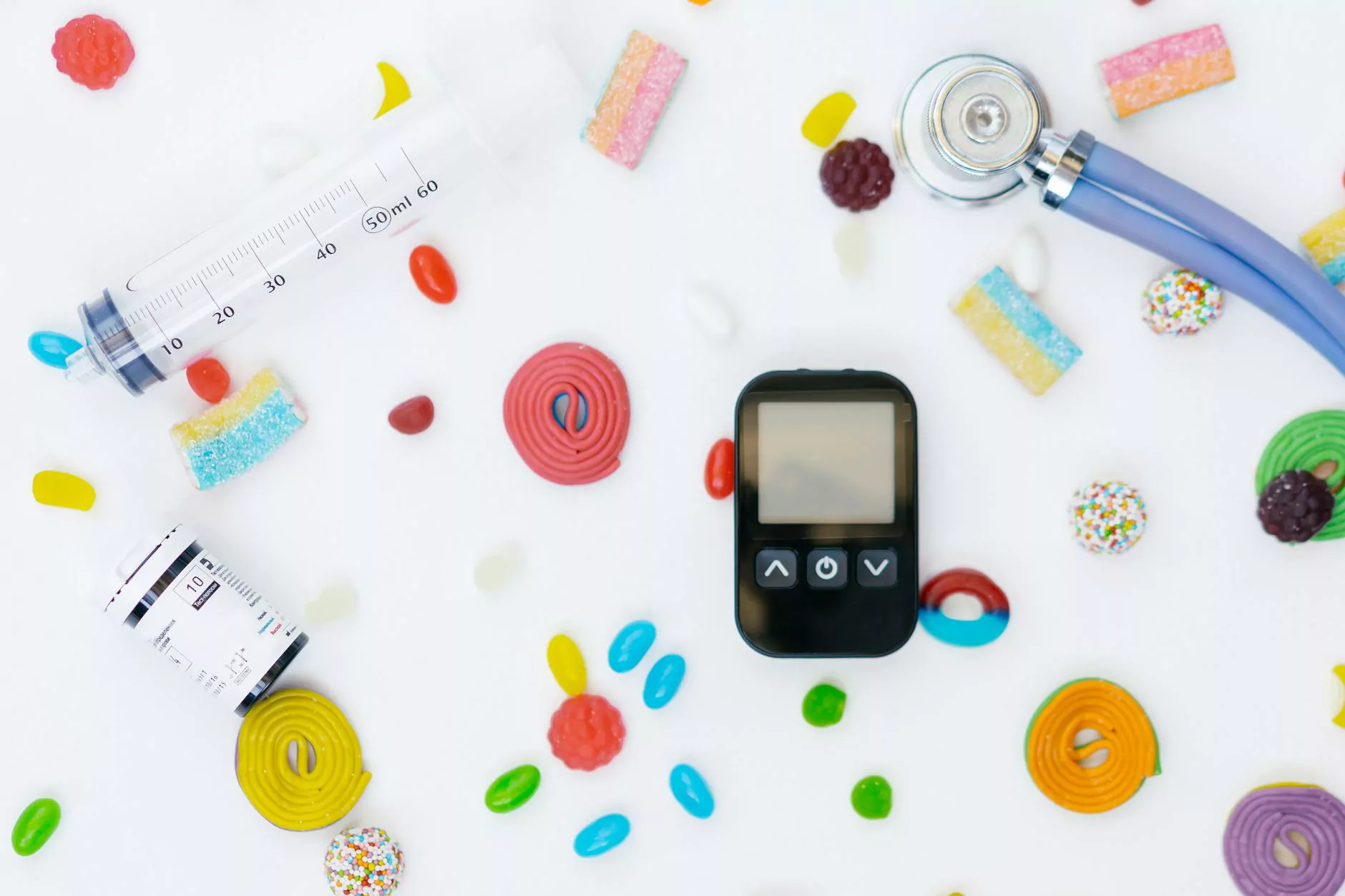
In the rapidly evolving landscape of metal fabrication, staying ahead with innovative machinery is crucial for enhancing productivity, precision, and sustainability. Among the forefront of technological advancements is the electric injection machine, a revolutionary tool that redefines traditional manufacturing paradigms. Whether you are a seasoned metal fabricator or a newcomer aiming to elevate your operations, understanding the intricacies and benefits of electric injection machines can unlock unprecedented opportunities for your business.
What Is an Electric Injection Machine? An In-Depth Overview
An electric injection machine is a sophisticated injection molding device that utilizes electric servo motors for the entire injection process, replacing traditional hydraulic systems. This transformation results in machines that are more energy-efficient, precise, and environmentally friendly, offering a compelling advantage for metal fabrication firms seeking sustainable growth.
Unlike conventional hydraulic injection molding machines, the electric injection machine employs high-precision servo drives, enabling meticulous control over injection speed, pressure, and position. This precision is vital in metal fabrication, where complex components demand tight tolerances and superior surface finishes.
Core Components and Features of an Electric Injection Machine
- Servo-Driven Ejection System: Ensures smooth, accurate ejection of finished metal parts without excessive force or wear.
- High-Precision Screw & Barrel Assembly: Facilitates flawless injection of molten metal with controlled temperature and pressure.
- Electric Servo Motors: Power the entire operation with precise control, minimal energy consumption, and reduced noise levels.
- Touchscreen Control Panel: Offers intuitive management of machine parameters, troubleshooting, and process optimization.
- Closed-Loop Control System: Maintains accurate operation through real-time feedback, ensuring consistency and quality.
Advantages of Choosing Electric Injection Machines for Metal Fabrication
1. Superior Energy Efficiency
One of the standout features of electric injection machines is their remarkable energy efficiency. Thanks to servo motors and minimal hydraulic components, these machines consume significantly less power, reducing operational costs and lowering carbon footprints. For metal fabricators committed to sustainability, this aspect is a game-changer.
2. Enhanced Precision and Consistency
Precision is paramount in metal fabrication, where even minor deviations can lead to costly rework or scrap. Electric injection machines excel in delivering consistent, high-quality outputs due to their highly accurate control systems. They facilitate tight tolerances, intricate moldings, and smooth surface finishes that meet stringent industry standards.
3. Greater Control and Flexibility
The advanced control features of electric injection machines enable manufacturers to fine-tune each process step. Adjustable parameters like injection speed, pressure, and cooling time allow for versatile processing of various metals and complex components, giving metal fabricators the flexibility to innovate and customize their production.
4. Reduced Maintenance and Increased Durability
Electric systems involve fewer moving parts subject to wear, leading to lower maintenance requirements and longer machine life. This translates to reduced downtime and higher overall productivity, vital for maintaining competitive edges in the fast-paced metal fabrication industry.
5. Environmental Benefits and Sustainability
In a world increasingly focused on environmental responsibility, electric injection machines align perfectly with green manufacturing goals. Their lower energy consumption, absence of hydraulic oil leaks, and reduced noise emissions contribute to safer and cleaner workplaces.
Applications of Electric Injection Machines in Metal Fabrication
These advanced machines are versatile and suitable for a wide array of metal fabrication applications, including:
- Production of precise metal components for automotive, aerospace, and electronics industries
- Manufacturing of complex die-cast parts with intricate details and tight tolerances
- Small to medium batch production requiring high flexibility and speed
- Prototyping and R&D projects where rapid adjustments and high precision are vital
- Custom metal parts for medical devices and precision instruments
Integrating Electric Injection Machines into Your Manufacturing Workflow
Successful integration requires strategic planning and proper training. Here are key considerations for optimizing your use of electric injection machines:
- Site Evaluation: Ensure your facility layout supports efficient workflow, including access for maintenance and material handling.
- Process Development: Collaborate with machine manufacturers or technical experts to develop optimal process parameters tailored to your specific metal types and product designs.
- Training and Skills Development: Invest in operator training to maximize machine capabilities and troubleshoot effectively.
- Maintenance Planning: Implement proactive maintenance schedules to prolong machine lifespan and maintain peak performance.
- Quality Control: Integrate inspection and testing protocols to harness the precision benefits of electric injection machines.
Choosing the Right Electric Injection Machine Supplier
Selecting a reliable partner like DeepMould ensures access to high-quality equipment, technical support, and customization options. When evaluating suppliers, consider:
- Reputation and industry experience
- Range of machine models and customization capabilities
- After-sales service and technical support
- Customer testimonials and case studies
- Availability of training and maintenance services
The Future of Metal Fabrication with Electric Injection Machines
As the industry adopts smarter, greener, and more efficient manufacturing technologies, electric injection machines will play an increasingly vital role. Emerging innovations such as IoT connectivity, predictive maintenance, and advanced automation will further enhance their capabilities.
Future developments are likely to focus on even higher energy savings, more adaptive control algorithms, and integration with Industry 4.0 platforms. Metal fabricators that embrace this technological evolution will gain a significant competitive advantage, delivering superior products faster and more sustainably.
Final Thoughts: Embracing Innovation for a Prosperous Future
The transition to electric injection machines signifies a strategic move toward smarter, more sustainable, and more profitable manufacturing. Their benefits—ranging from precision and efficiency to environmental sustainability—make them indispensable tools for modern metal fabricators. Partnering with industry leaders like DeepMould ensures your business is equipped with cutting-edge machinery and expertise, paving the way for sustained growth and excellence in metal fabrication.
By investing in electric injection machines, your manufacturing processes will not only meet but exceed the evolving demands of global markets, positioning your company as a leader in high-quality metal fabrication solutions.